News & Events
Roto-Molding Rocks, But What Is It?
At Tonik, we talk a lot about rotational molding. It’s because we’re particularly proud of the advanced technological process that we’ve refined over the years.
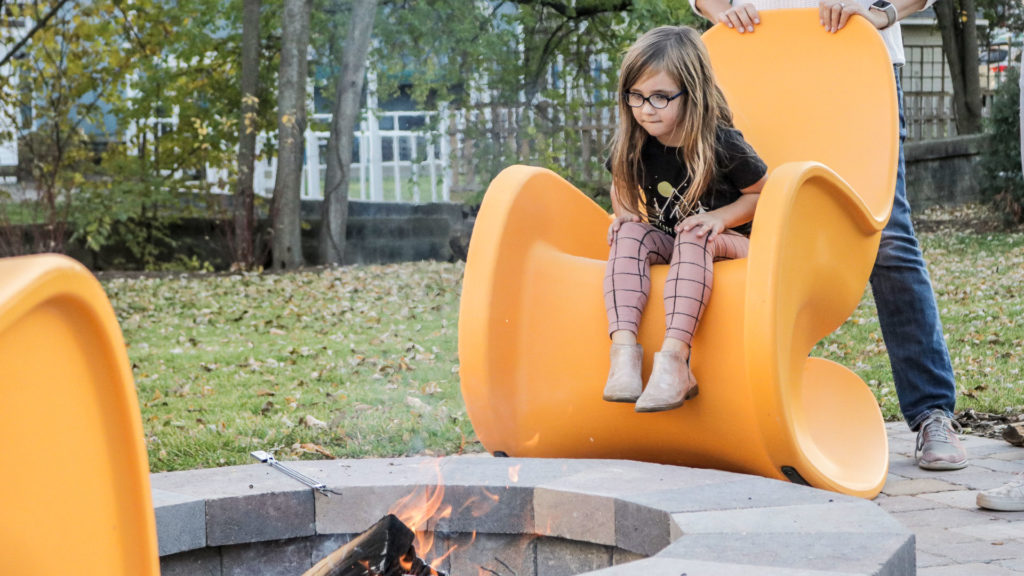
Rotational molding, or roto-molding, isn’t a new idea. In fact, an 1855 patent taken out by R. Peters in Britain documented the first use of a rotating mechanism as a means of production. Of course, this was well before plastics were invented, so creating yummy treats like hollow chocolate easter eggs was a purpose of the technology.
In the 1950s, rotational molding took on plastics in complex shapes such as polymer doll heads. In the 1980s, new plastics such as polycarbonate, polyester, and nylon were used to create heavy-duty items such as fuel tanks. You may have used modern-day roto-molded products such as a brand-name popular cooler known for its durability.
The clear benefit of roto-molding is the ability to control wall thickness. Thicker walls are costlier and more time-consuming to make but increase the overall durability of the end-product. Other molding technology often stretches the material. Corners and bends are not as thick as other parts. The result of roto-molding creates inherent design strengths such as strong outside corners that are virtually stress-free. Parts such as metal threads can be securely molded directly into the furniture.
The rotational molding process of Dottie
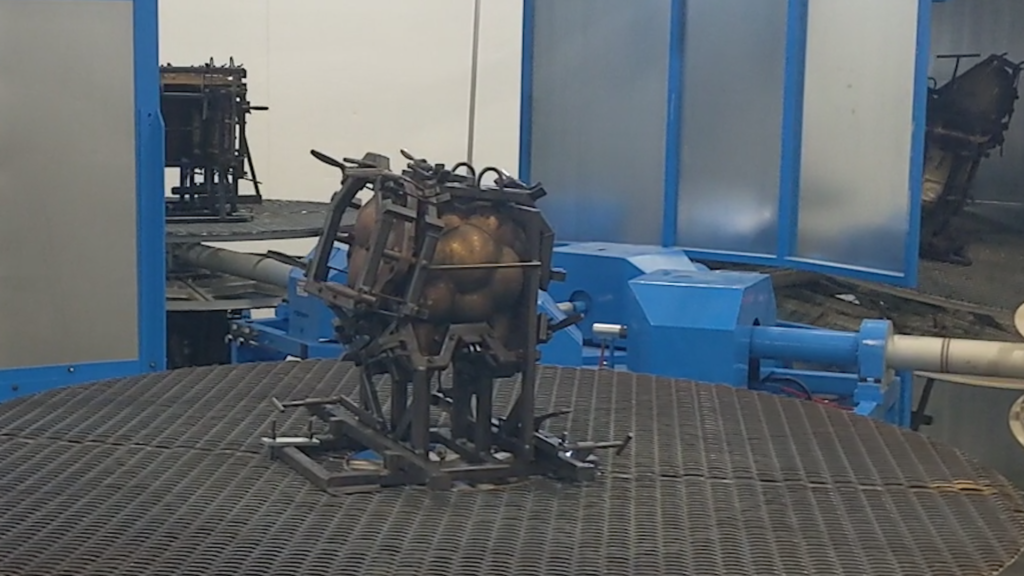
- The Dottie mold is loaded with a measured quantity of powder polymer.
- Dottie mold is heated in an oven while it rotates until all the polymer has melted and adhered to the mold wall. The hollow part is rotated through two axes, rotating at different speeds to ensure every curve is evenly covered. Dottie’s time in the oven is critical: too long, and the polymer will degrade, reducing impact strength. If Dottie spends too little time in the oven, the polymer melt may be incomplete.
- Dottie gets to chill out in a cooling phase. The polymer must be cooled so that it solidifies and can be handled safely by the operator. The cooling rate must be kept within a certain range. Very rapid cooling (for example, water spray) would result in cooling and shrinking at an uncontrolled rate, producing a warped part.
- Removal of Dottie and inspection.
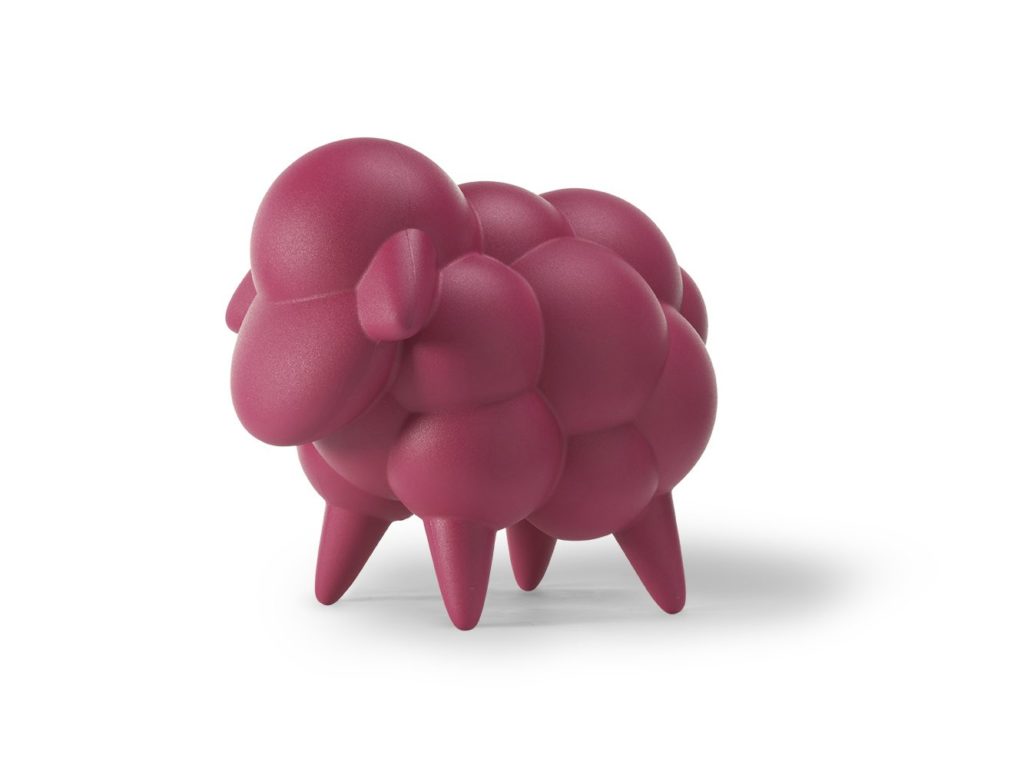
Roto-molding isn’t fast and easy, but it’s the only process that ensures we have full control and confidence in our products. This complex balance of material, heating, and cooling are what makes our products Tonik tough.
Want to see it in action? Watch this short video on “What is Rotational Molding.”